What You Don't Know Will Hurt You.
- wcmccranie
- Apr 21
- 3 min read
Unrecognized and unresolved issues snowball through a facility leading to poor performance and employee dissatisfaction. Work harder, not smarter. Labor costs and excessive employee turnover are two of the most glaring results. And turnover costs are certainly measurable!
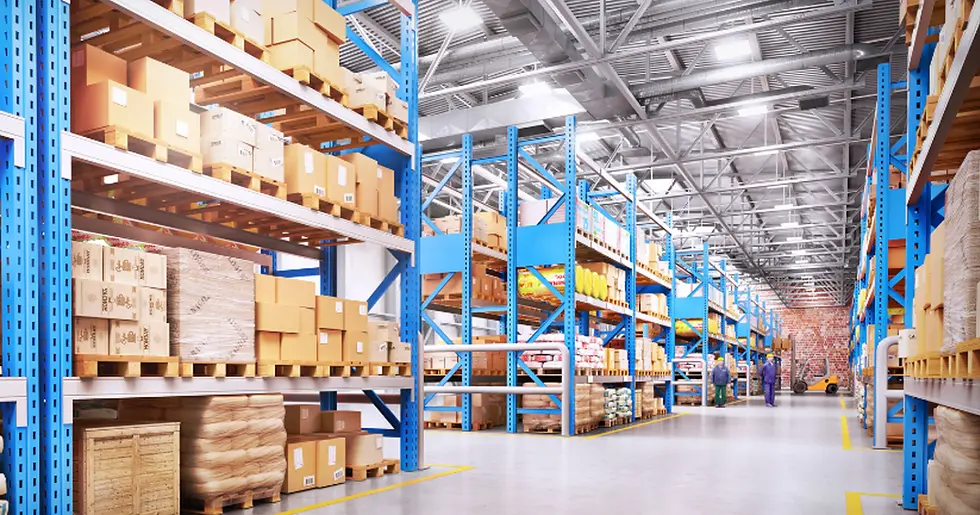
An Overlooked Approach to Improve Facility Performance
There are often overlooked issues that go unaddressed and impact negatively the performance in a facility. Addressing the issues noted in this article is essential! Failure to address them snowballs, resulting in the present state of your facility. No matter the size of a company, these issues exist at an alarming rate. Supervisors and managers, due to daily pressures and demands on their time, are tunnel-visioned to getting the necessary things done daily to get product through the building and out the door. Little action is taken on the status quo! Whatever it takes to get it done, along with what they deem to be acceptable error rate, inventory accuracy, product damages, safety and labor cost. They also lack the expertise and time to address the issues and can be even unaware many exist. But how much better could the facility perform (including tangible labor savings) if the issues discussed in this article are transformed to being areas of excellence?
Transform the Productivity of Your Facility
W. Edwards Deming, a renowned American industrial expert and management consultant said 90% of all problems were managements’ responsibility and the workers were ultimately responsible for 10%. Sounds crazy on the surface, right? Maybe not that high? Perhaps. Consider, for example, an employee making an error and failed to follow “the process”. He or she is to blame. Really? Are there even properly defined instructions for tasks? Was their training deficient without the documentation for the processes? Was the employee just put with someone else doing the job and informally trained? A culture of allowing employees to do things how they want to? Not having the right tools to do the job?
Performance Issues That Must be Addressed
Poor performance regarding issues related to quality, accuracy, labor costs, job satisfaction, and employee turnover raises its ugly head in the following ways:
· Poor processes established in the first place.
· Failure to follow processes by employees.
· Inadequate training program for employees, along with periodic follow-up.
· Unprofessional supervisors that lack management skills.
· Safety issues unaddressed that cause minor injuries that aren’t documented and, of course, loss-time accidents.
· Difficulty for employees handling product where simple material handling equipment and tools would help immensely.
· Employees are having to work harder and not smarter.
· Management blaming employees for errors or poor performance when management fails to see the root cause.
· Employees experience negativity, irritation, frustration and feel management doesn’t care about them.
· Employee turnover associated with the above bullet points is excessive. NOTE: The cost of employee turnover is measurable!
What now?
See how the above can snowball? I have the knowledge and expertise to assess the above issues and other areas of concern and provide recommendations to improve performance dramatically. A brief 2 day assessment is all that is needed:
· Assess your facility related to issues such as those in this article.
· Discover opportunities to increase capacity.
· Observe existing processes to reveal opportunities to attain labor savings and streamline flow through the building.
· Recognize low-hanging fruit for immediate improvements.
From the assessment, it will be clear what needs to be addressed. And should you desire, I am ready to help you make the changes needed to raise your performance.
Contact me to provide you with this approach to consulting.